7 Barons Behind Famous Beers
By Ethan Trex
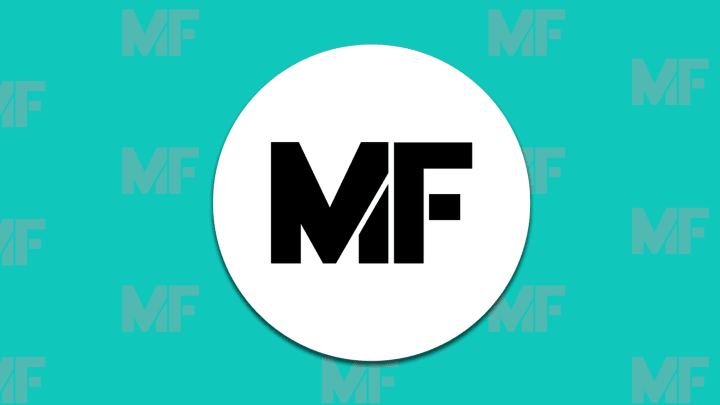
A number of the American brewing industry's pioneers led fairly colorful lives before and after getting their surnames emblazoned on cans and tap handles. Here's the scoop on a few of the wisest men to ever ferment a little barley. Remember: when in doubt, always marry your former boss' widow.
1. Eberhard Anheuser
Anheuser wasn't actually a brewer. Instead, he was a successful soap factory owner in St. Louis just before the Civil War. Anheuser provided a good deal of cash to the owners of the struggling Bavarian Brewery, which opened in 1852, and he eventually ended up acquiring the brewery in 1860 as repayment for these debts. The soap baron promptly renamed his new beer concern E Anheuser & Co.
2. Adolphus Busch
The other name in the Anheuser-Busch empire didn't set out with huge dreams of being a brewer, either. Busch arrived in St. Louis in 1857 as an industrious 18-year-old German immigrant who was the second youngest of 22 siblings. Busch found work as a commission salesman, and within two years, he and a partner moved on to a more lucrative field when they opened their own brewing supply wholesaler. Busch was able to brush up on brewing practices through his new business, and he also became quite partial to Lily Anheuser, the aforementioned Eberhard's daughter. When Busch married Lily in 1861, he became a part of the brewer's family, and in 1879 the company's name officially became Anheuser-Busch.
Busch wasn't just a guy who married well, though. He was the first American brewer to pasteurize his brews in the 1870s, and his ingenious development of a network of icehouses next to railroad tracks enabled Busch to ship his beer nationally while keeping it cold and fresh.
3. Adolph Coors
In 1868, Coors came to America as an industrious young brewer's apprentice. By 1873, his search for suitable water for brewing had led Coors to Golden, Colorado, where he opened the Golden Brewery in a partnership with Jacob Schueler. Schueler put up most of the cash; he invested $18,000 to just $2,000 from Coors. Why aren't we all going out for an extra case of Schueler's, then? Because the partnership didn't last too long. Coors bought out Schueler in 1880. Coors wasn't just a brewer, though.
When Prohibition came to Colorado in 1916, three years before the rest of the country went dry, he kept the business afloat by making malted milk and focusing on the family's ceramics business, which is now known as CoorsTek, one of the world's largest industrial ceramics companies.
4. Frederick Pabst
Wikimedia Commons
The man behind PBR was also a German immigrant who came to the United States as a young boy. The Pabst family lived in Chicago, where Frederick worked as a waiter, cabin boy, and eventually a captain on steamships that cruised through Lake Michigan. Unfortunately for Pabst, he didn't win any blue ribbons as a sailor; an 1863 storm caused him to rack up $20,000 worth of damage when he beached his ship. Pabst was so frustrated and scared by the wreck that he gave up sailing altogether.
Luckily, though, Pabst's father-in-law was a Milwaukee brewer who helped the former sailor find a new calling. Although Pabst didn't know anything about brewing, he took at job at the family's Best Brewery, and within a few years had bought out his father-in-law with some help from his brother-in-law.
Once they took over, the two started expanding the brand nationally with a little help from some clever marketing. Armed with the prestige of awards that his beer won at the Philadelphia Centennial Exhibition in 1876 and the 1878 Paris World's Fair, Pabst started putting little blue ribbons around the neck of each bottle. When the brew grabbed another award at the 1893 Columbian Exhibition in Chicago, the name changed for good, and Pabst Blue Ribbon was born.
5. Joseph Schlitz
Schlitz knew how to make a quick rise through a company. In 1856, he was the manager and bookkeeper of August Krug's brewery in Milwaukee. When Krug died, Schlitz married his former boss' widow and renamed the brewery the Joseph Schlitz Brewing Company.
When the Great Chicago Fire ravaged the city in 1871, Schlitz made a unique donation to the recovery effort: hundreds of barrels of beer for thirsty Chicagoans.
This move helped spike the brand's popularity in one of the country's major markets and made Schlitz even wealthier. Sadly, he met a tragic end while traveling to a sharpshooting contest in his native Germany; Schlitz was aboard the steamship Schiller when it sank off the coast of England.
6. Valentin Blatz
Schlitz wasn't the only brewer who learned the value of marrying a widow. The brewery modern drinkers know as Blatz was originally called the City Brewery and was owned by a brewer named John Braun. Braun's fledgling business took a bit of a dip in 1851 when a former employee named Valentin Blatz opened up a brewery of his own—right next door. Braun died within a year, and Blatz soon married the widow and united the two breweries, which quickly grew from a pair of tiny concerns into a single brewing giant.
7. Frederick Miller
Unlike some of his beer-slinging counterparts, Miller didn't have to come to the States to get his start as a brewer. Miller was already pretty successful as a brewer back home in Germany when he came to Milwaukee in 1854. A year later, he leased the Plank Road Brewery in Milwaukee and started brewing with yeast he'd brought with him all the way from Germany. By 1883, Miller was doing his own bottling, too, and the man whose company brought you Miller Lite and taught you how to live the High Life was established as a brewing titan on this side of the pond, too.
This post originally appeared in 2009.